Lassen
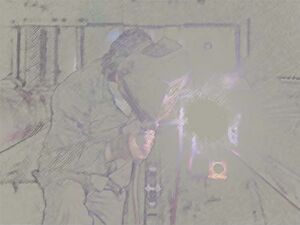

Lassen is het verbinden van materialen door druk en/of warmte, waarbij het materiaal op de verbindingsplaats in vloeibare of deegachtige toestand wordt gebracht (hoewel er ook uitzonderingen zijn, zie kouddruklassen), terwijl al of niet materiaal met ongeveer dezelfde samenstelling wordt toegevoegd, waarbij continuïteit ontstaat tussen de te verbinden delen.
Anders dan bij solderen smelt bij lassen ook het materiaal van het werkstuk, dus niet alleen het toevoegmateriaal.
Geschiedenis
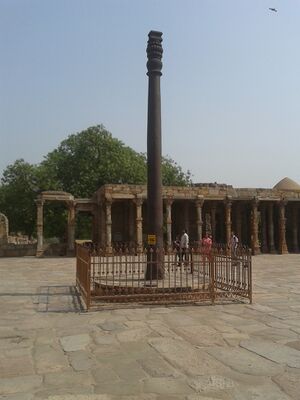
De eerste sporen van lassen dateren uit de Bronstijd en de IJzertijd in Europa en het Midden-Oosten. De oude Griekse geschiedschrijver Herodotus beschreef in de 5e eeuw voor Christus in de 'Historiën' dat Glaucus van Chios de man was die eigenhandig het lassen van ijzer had uitgevonden. De techniek van het lassen werd gebruikt bij de constructie van de ijzeren pilaar in Delhi, India, die rond 310 n. Chr. werd gebouwd en 5,4 ton woog. [1]
In de middeleeuwen was smeden, waarbij een smid ijzer net zo lang hamerde totdat de delen aaneen verbonden werden, het enige lasproces. Daarin werden geleidelijk vorderingen gemaakt, en in 1540 publiceerde Vannoccio Biringuccio het eerste Europese boek dat zich bezighield met smeden en metallurgie: De la Pirotechnia. De vaklieden uit de Renaissance waren zeer geoefend in het proces, en de industrie groeide hard tijdens de volgende eeuwen. In 1801 ontdekte Sir Humphry Davy de kort gepulste elektrische boog en een jaar later vond de Russische wetenschapper Vasily Petrov onafhankelijk daarvan de continu stabiele elektrische boog uit. Dankzij daaropvolgende ontdekkingen tijdens die eeuw zou booglassen de meest gebruikte vorm worden van het metallurgisch verbinden van metalen.
In 1865 werd een Engelsman genaamd Wilde het eerste patent op een lasproces toegewezen. De elektrische boog kreeg pas praktische toepassingen rond 1881, toen de Rus Nikolaj Benardos de eerste bruikbare booglastechniek uitvond, met elektroden van koolstof. Tijdens dat decennium werd er veel vooruitgang geboekt in de booglasprocessen, waaronder het gebruik van een metalen elektrode (in plaats van koolstof) en een geïsoleerd handvat, waardoor er handmatig gelast kon worden (door Benardos gepatenteerd in 1887). Rond 1900, werd door A.P. Strohmenger een beklede elektrode bedacht, die een stabielere boog gaf. Daaropvolgend werden er twee nieuwe lasprocessen ontwikkeld in de laatste twee decennia van de 19e eeuw, namelijk weerstandlassen en autogeen lassen. Autogeen lassen was aanvankelijk populairder vanwege de compactheid en relatief lage kosten. Maar in de loop van de 20e eeuw verdween het langzaam uit de industrie. Het werd grotendeels vervangen door booglassen, daar elektrodebekledingen werden ontwikkeld die de boog stabiliseerden en materiaal beschermden tegen onvolkomenheden.
In de jaren 1920-'30 werd lassen steeds meer gebruikt. De toepassing van bekledingen werden steeds goedkoper toen in 1927 een extrusieproces werd ontwikkeld. Deze ontwikkeling leidde tot een enorme toename van de rol van booglassen in de jaren 1930-'40 en in de Tweede Wereldoorlog. Tijdens deze jaren werden er verschillende grote ontdekkingen gedaan in het gebruik van automatisch lassen, lassen met wissel- en gelijkstroom en bekledingstypen. In 1930 werd het stiftlassen uitgevonden, in 1932 werd voor het eerst onderwater gebooglast, en ook werd er voor het eerst geëxperimenteerd met het gebruik van inerte beschermgassen, om onedele metalen als aluminium en magnesium te kunnen lassen. Dat leidde weer tot de uitvinding in 1948 van de nieuwe lasprocessen: TIG-lassen en het verwante plasmalassen.
De Tweede Wereldoorlog bracht een grote toename in het gebruik van lasprocessen teweeg. De verschillende militaire machten probeerden te bepalen welk proces het beste was. De Britten gebruikten voornamelijk booglassen. Ze hebben zelfs schepen gebouwd met compleet gelaste romp (wat uitzonderlijk was voor die tijd) genaamd de Libertyschepen. Ze hebben nog tot jaren na de oorlog dienstgedaan als koopvaardijschepen. Tegenwoordig worden alle schepen gelast in plaats van geklonken. De Amerikanen twijfelden in eerste instantie, maar begonnen de voordelen van lassen in te zien toen het proces hen in staat stelde om snel hun schepen te repareren na een Duitse aanval op de haven van New York.
Een van de beperkingen van TIG-lassen is dat het een lage neersmelt (in gewicht) per tijdseenheid heeft en dus niet erg geschikt om zware lassen te maken. Dit leidde tot de ontwikkeling van een proces met constant toegevoerde draad, MIG/MAG-lassen, aangekondigd in 1948. Tijdens deze periode werden enkele belangrijke ontdekkingen gedaan, zoals het gebruik van metaalpoeder in de mantel van beklede elektroden, het gebruik van argon/helium gasmengsels en uiteindelijk het gebruik van het veel goedkopere kooldioxide. In 1958 debuteerde het lasproces met gevulde draad, waarmee de zelfbeschermende draadelektrode gebruikt kon worden zonder of met weinig gas en automatische apparatuur, wat resulteerde in een toename van de lassnelheden (lees neersmelt).
Lasprocessen
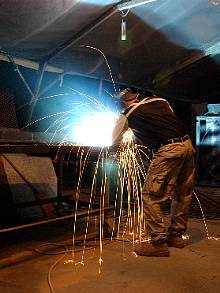

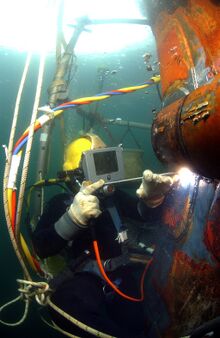
Er zijn in de loop van de tijd veel verschillende lasprocessen ontwikkeld, alle met specifieke kenmerken en toepassingsgebied. Grofweg kunnen ze ingedeeld worden in 6 hoofdgroepen (waarbij de laatste groep: groep 7, een 'verzamelgroep' is).
Vanwege de uitgebreidheid van het onderwerp worden deze groepen en de aparte lasprocessen beschreven in aparte artikelen, die bereikbaar zijn via onderstaand schema:
| Lasproces De nummers bij de lasprocessen zijn conform EN ISO 4063 (2009) [2] | |
---|---|
1. booglassen |
11. elektrisch booglassen zonder gasbescherming: 12. Onder Poederdek (OP)-lassen 15. plasmalassen |
2. elektrisch weerstandlassen |
21. puntlassen |
3. autogeen lassen |
31. autogeen lassen met zuurstof-brandstof-gasmengsel
32. autogeen lassen met lucht-brandstof-gasmengsel |
4. druklassen |
41. ultrasoon lassen 43. wrijvingsroerlassen
45. diffusielassen |
5. bundellassen | |
7. andere lasprocessen |
71. exothermisch lassen (thermietlassen) |
Voor- en nadelen van lasverbindingen
- Voordelen
- Lasverbindingen zijn heel sterk, licht en stijf.
- Lasverbindingen zijn vaak eenvoudiger, goedkoper en sneller (geautomatiseerd) te realiseren dan andere verbindingstechnieken zoals bout- of klinkverbindingen waarbij gaten geboord dienen te worden en waarbij monteren langer duurt. Bovendien sneller dan lijmverbindingen, omdat een lasverbinding niet hoeft te drogen of harden.
- Gladde oppervlakken; dit is o.a. belangrijk voor de binnenkant van pijpen vanwege stromingsweerstand en in de farmaceutische en levensmiddelenindustrie vanwege hygiëne.
- Bestand tegen hoge temperaturen.
- Goede krachtoverdracht, geen verzwakking van de constructie, in tegenstelling tot klinknagels en bouten ('perforatie-effect').
- Nadelen
- Lasverbindingen zijn niet demonteerbaar.
- Bij het lassen treedt structuurverandering van gelaste materialen op, wat een verandering in de mechanische eigenschappen (sterkte, hardheid) van het materiaal ter plaatse van de las veroorzaakt. (Zie ook: Warmte-beïnvloede zone.)
- Het lasproces kan een negatieve invloed uitoefenen op de directe omgeving, bijvoorbeeld vanwege de vrijkomende hitte, rook, spatten, slak of vanwege gebruikte (toevoeg-)middelen. Er kunnen daardoor ook gezondheidsrisico's verbonden zijn aan het lassen.
- Lassen en daarmee gepaard gaande sterke opwarming en afkoeling veroorzaakt krimp en daardoor vervorming.
- Met de meeste lasprocessen kunnen alleen min of meer gelijke materialen aan elkaar gelast worden.
Materialen
Lasbare materialen
Dankzij alle technologische ontwikkelingen binnen de laswereld kan inmiddels een enorm groot aantal materialen gelast worden. Hieruit blijkt dat het een voorwaarde is dat de materialen smeltbaar zijn. Daarom is het onmogelijk niet-smeltbare materialen, zoals thermohardende kunststoffen te lassen. Soms is er meer mogelijk dan men zou verwachten, want het is zelfs mogelijk gebleken om keramiek [3] en hout [4] te lassen. Het is onder bepaalde voorwaarden ook mogelijk om ongelijke materialen aaneen te lassen.
Wel vereisen sommige materialen speciale voorzorgsmaatregelen, bijvoorbeeld voorverwarmen, speciaal toevoegmateriaal of een warmtebehandeling achteraf. Ook zijn lang niet alle lasprocessen bruikbaar voor alle materialen.
Staal is wel de meest gebruikte maar ook roestvast staal en non-ferrometalen (zoals aluminium) en zelfs vele kunststoffen zijn uitstekend lasbaar. Voorbeelden van lassen met niet-metalen zijn:
- thermoplastische kunststoffen: o.a. spiegellassen, inductielassen, wrijvingslassen en ultrasoon lassen
- glasvezels: fusielassen
Maar zelfs het aan elkaar vast laten vriezen van stukken ijs of het aan elkaar smelten van plakjes kaas zou vanuit deze optiek als lassen beschouwd kunnen worden.
Toevoegmaterialen
Lassen is in de praktijk meestal veel méér dan alleen smelten en weer laten stollen. Het is mogelijk het lasproces te beïnvloeden door allerlei toevoegmaterialen, die verschillende functies kunnen hebben.
Functies van toevoegmaterialen kunnen zijn:
- Bescherming: Door de hitte tijdens het lasproces kunnen ongewenste chemische reacties optreden, zoals verbranding. Door gebruik van beschermgas, laspoeder of de bekleding of vulling van de lasdraad is het mogelijk dit te voorkomen.
- Verbetering van het lasproces: Door goede keuze van toevoegmaterialen is het mogelijk de stabiliteit van een lasboog te verbeteren, een diepere of juist minder diepe inbranding te bewerkstelligen.
- Beïnvloeding van het smeltbad: bij verticaal of bovenshands lassen is het belangrijk dat het smeltbad niet wegdruipt. Ook is het vaak wenselijk dat de las meteen mooi glad trekt, zodat geen nabewerking nodig is. De keus van een beschermgas kan hierbij een rol spelen, en bij lassen met beklede elektrode kunnen stoffen in de bekleding hierop van invloed zijn.
- Kwaliteitsverbetering: Door hoge temperaturen kan het bij het lassen van legeringen (bijvoorbeeld roestvast staal) gebeuren dat bepaalde stoffen oxideren of uit het smeltbad verdampen, waardoor de samenstelling en daardoor de kwaliteit van het materiaal vermindert. Toevoegmaterialen kunnen dat compenseren doordat zij opzettelijk een hoger gehalte van die stoffen bevatten.
- Verwerkbaarheid: Lasdraad wordt vaak bekleed met een dun laagje koper, ter bescherming tegen corrosie, als glijmiddel tijdens transport (MIG/MAG-lassen) en voor verbetering van elektrisch contact.
Kwaliteit
De kwaliteit van de las wordt bepaald door vele factoren. Dit begint al met het uitgangsmateriaal en de eventuele toevoegmaterialen. Het materiaal in de omgeving van de las verandert door het lasproces; meestal op een ongunstige manier. Deze veranderingen komen met name voor in de z.g. 'warmte-beïnvloede zone'.
Een andere belangrijke factor bij de kwaliteit van lassen zijn lasfouten.
De laatste decennia is het accent van ontwikkelingen in de laswereld vooral komen te liggen op kwaliteitsverhoging. Dit kan gebeuren door het ontwikkelen van specifieke lasprocessen, maar gebeurt vooral door het optimaliseren van de bestaande processen en de opleiding van lassers. Kwaliteitscontrole van lassen gebeurt vaak door middel van röntgenonderzoek of bijvoorbeeld met ultrasone apparatuur. Er zijn nog vele andere onderzoeksmethoden. Zij hebben alle tot doel naar het inwendige van de las te kijken. Dit noemt men niet-destructief onderzoek (n.d.o.). In die gevallen waar n.d.o. niet toepasbaar is wordt ook wel destructief onderzoek gebruikt. Men last dan bijvoorbeeld proefstroken mee waar dan buigproeven / trekproeven enz. van kunnen worden gemaakt.
Veiligheid
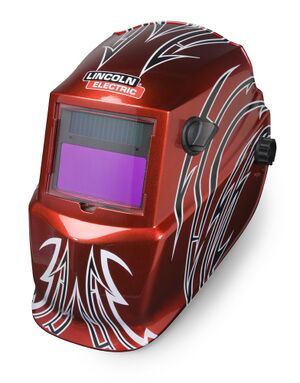
Bij het lassen is, zoals bij ieder ander productieproces, de veiligheid van groot belang.
Vonken en gloeiende metaalspetters kunnen brandplekken geven. Daarom zijn lange handschoenen en eventueel een beschermend schort nodig. Ook mag er geen brandbaar materiaal in de omgeving liggen.
Bij elektrische lasprocessen is het mogelijk elektrische schokken en brandwonden te krijgen. Het is daarom belangrijk dat handschoenen en ook schoenen goed isoleren.
Er komen ook schadelijke gassen vrij (onder andere ozon en lasrook). Voorts kunnen gebruikte beschermgassen ongemerkt zuurstof verdringen. Het heeft daarom de voorkeur dat er geforceerde ventilatie is.
Een plasmaboog geeft een zeer fel licht af, met vooral schadelijke uv-stralen. Een laskap met een donker glaasje beschermt de ogen (Zie Lasoog) en het gezicht. De donkere gradatie van het lasglaasje (shade) wordt weergeven in een getal. Deze lasglaasjes zijn naar sterkte genummerd. De nummering loopt van 4 tot 16. Hoe hoger het nummer, hoe meer straling wordt geabsorbeerd (gefilterd). Het juiste filter (shadenummer) wordt gekozen afhankelijk van de gebruikte stroomsterkte. In de tabel hieronder wordt weergegeven welke gradatie gebruikt moet worden.
Materiaal | Lasstroom (A) | Shadenummer |
---|---|---|
Staal | tot 40 | 9 |
Staal | 40 - 80 | 10 |
Staal | 80 - 175 | 11 |
Staal | 175 - 300 | 12 |
Staal | 300 - 500 | 13 |
Aluminium | 80 - 100 | 10 |
Aluminium | 100 - 175 | 11 |
Aluminium | 175 - 250 | 12 |
Aluminium | 250 - 350 | 13 |
Aluminium | 350 - 500 | 14 |
Overigens is bij sommige lasprocessen (met name bij TIG-lassen) de uv-straling zo sterk dat ook de huid beschermd moet worden om verbranding te voorkomen.
Lasverbindingen

Geometrisch gezien kunnen lassen op vele manieren worden gemaakt, maar ze zijn in te delen in verschillende hoofdgroepen: stuiklas (of kopse las), overlaplas, oplas, T-las, hoeklas, flenslas.
Sommige lastechnieken vereisen specifieke verbindingsvormen, terwijl andere lastechnieken vrijwel elke verbindingsvorm kunnen lassen.
Bij bepaalde technieken (bv. lassen met beklede elektrode, MIG/MAG-lassen) is het wenselijk dat dikke materialen vooraf afgeschuind worden, waarbij deze V-naad soms in meerdere lagen opgelast wordt. Bij andere technieken (onder andere die waarbij de keyhole lastechniek wordt gebruikt), is juist een stompe verbinding vereist.
Een bijzondere techniek die gebruikt wordt als een oplas of een overlaplas moet worden gemaakt waarbij het gebruikte lasproces niet in staat is een voldoende doorlassing te verkrijgen, is gat- of proplassen. Daarbij worden op regelmatige afstanden gaten in het op te lassen werkstuk gemaakt, die vervolgens worden dichtgelast.
Externe links
- Belgisch Instituut voor Lastechniek
- Nederlands Instituut voor Lastechniek
- Brits instituut voor lastechniek
Zie ook
- Metaalconstructies, cursustekst A. Dhooge, UGent
- ↑ (Engels) Cary, Howard B; Helzer, Scott C. (2005). Modern Welding Technology. Upper Saddle River, New Jersey: Pearson Education. ISBN 0-13-113029-3.
- ↑ Er is in de ISO-systematiek geen hoofdgroep (meer?) met het nummer 6. De hoofdgroepen 8 en 9 worden niet gebruikt voor de indeling van lassen: hoofdgroep 8 wordt gebruikt bij de indeling van snijden en gutsen; hoofdgroep 9 bij de indeling van solderen en soldeerlassen.
- ↑ (Engels) US patent: Ceramic welding process
- ↑ Hout lassen door wrijving - Houtnieuws.be. Gearchiveerd op 31 augustus 2021.